Oli Free Air Compressor
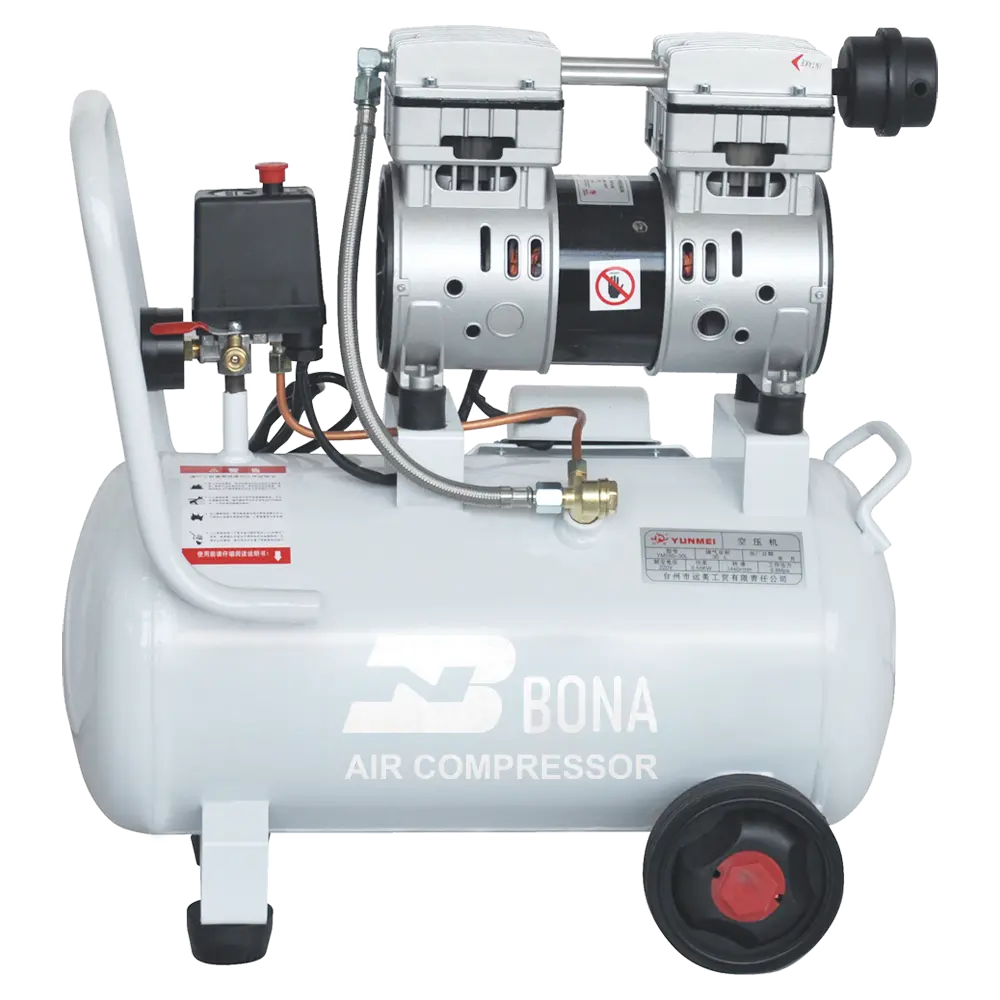
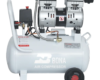

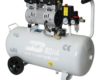
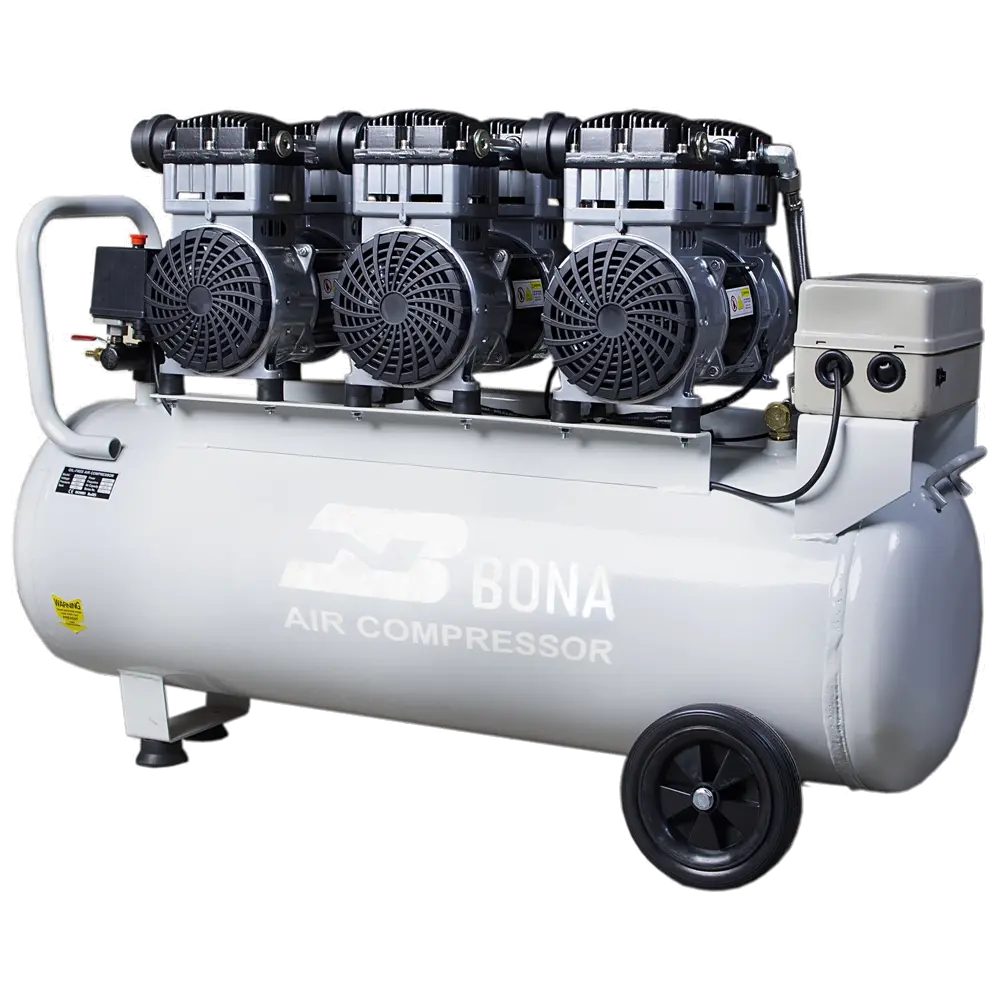
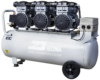
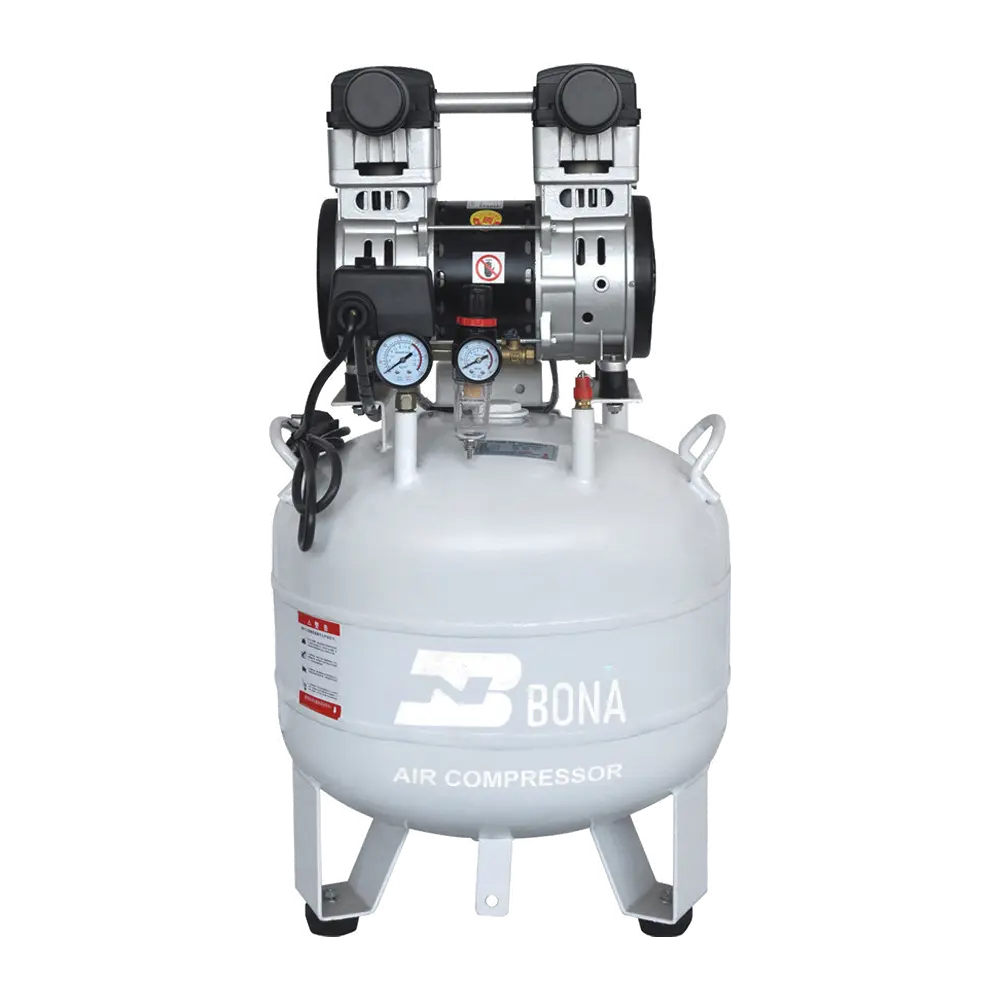
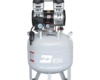
Our Advantage
Oil-free compressors are also significantly lighter than oil-lubricated compressors, making them ideal for commercial applications that require portability, such as tire inflation, jackhammering, medical air supplies, and roadside assistance pneumatic tools.
Oiled compressors, on the other hand, are bulkier, heavier, and often require mounting. This makes them better suited for situations where the equipment does not require frequent relocation.
Product Description
Multiple Applications
- Medical and Pharmaceutical – In medical and pharmaceutical applications, cleanliness is a critical factor in the quality and performance of the products. The product or manufacturing process will often dictate the risk tolerance for any trace contaminants such as oil or moisture.
- Food and Beverage – New requirements outlined in the FDA’s Food Safety Modernization Act, Global Food Safety Initiative, and British Compressed Air Society Code of Practice, reinforce the need for using clean air in the manufacturing process to avoid product contamination, which can lead to product recalls and a damaged brand reputation.
- Electronics – For applications including PC board cleaning, delivering clean, dry compressed air is critical to minimizing trace contaminants in the end product. Requiring the highest class in air purity allows manufacturers to protect sensitive instrumentation and their finished products.
- Textiles– A quality stream of compressed air for spinning machines and air-jet looms is crucial to prevent fabric staining and production loss. Mandating the highest class of air purity is essential for delivering high quality, oil-free, manufactured products.
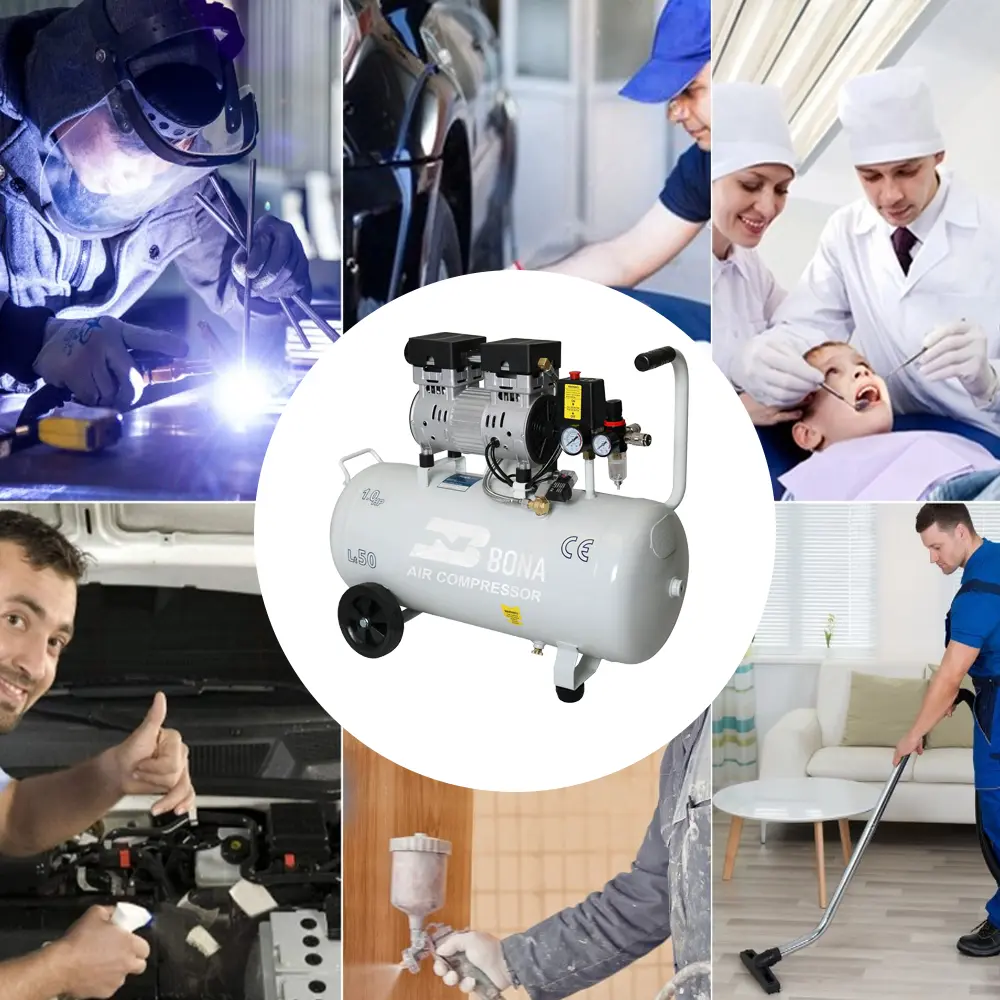
Reduce Maintenance Costs
- Fewer ancillary air system components to maintain.
- Longer timeframes between oil changes.
- Elimination of expensive oil filters to clean the compressed air.
- Elimination of oily condensate management.
- Longer desiccant life of downstream air filters.
- Minimized downstream labor and outage-related costs.
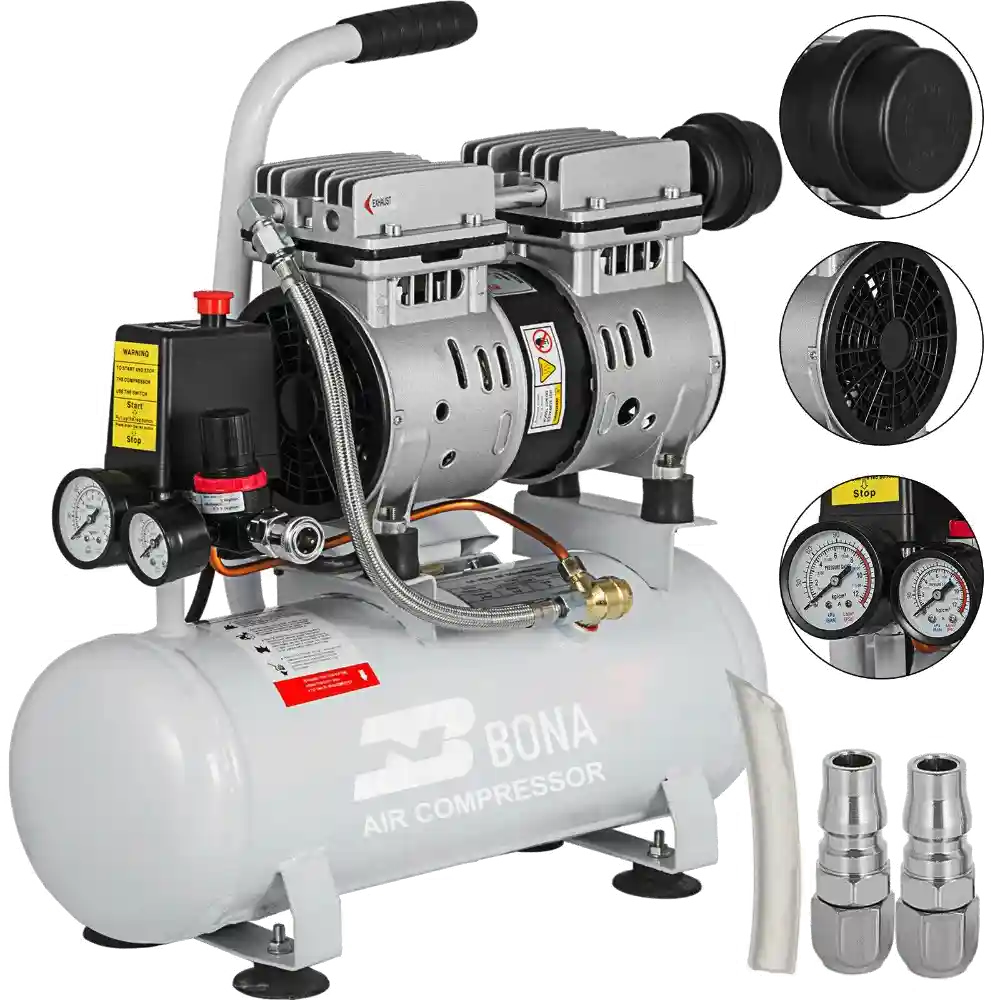
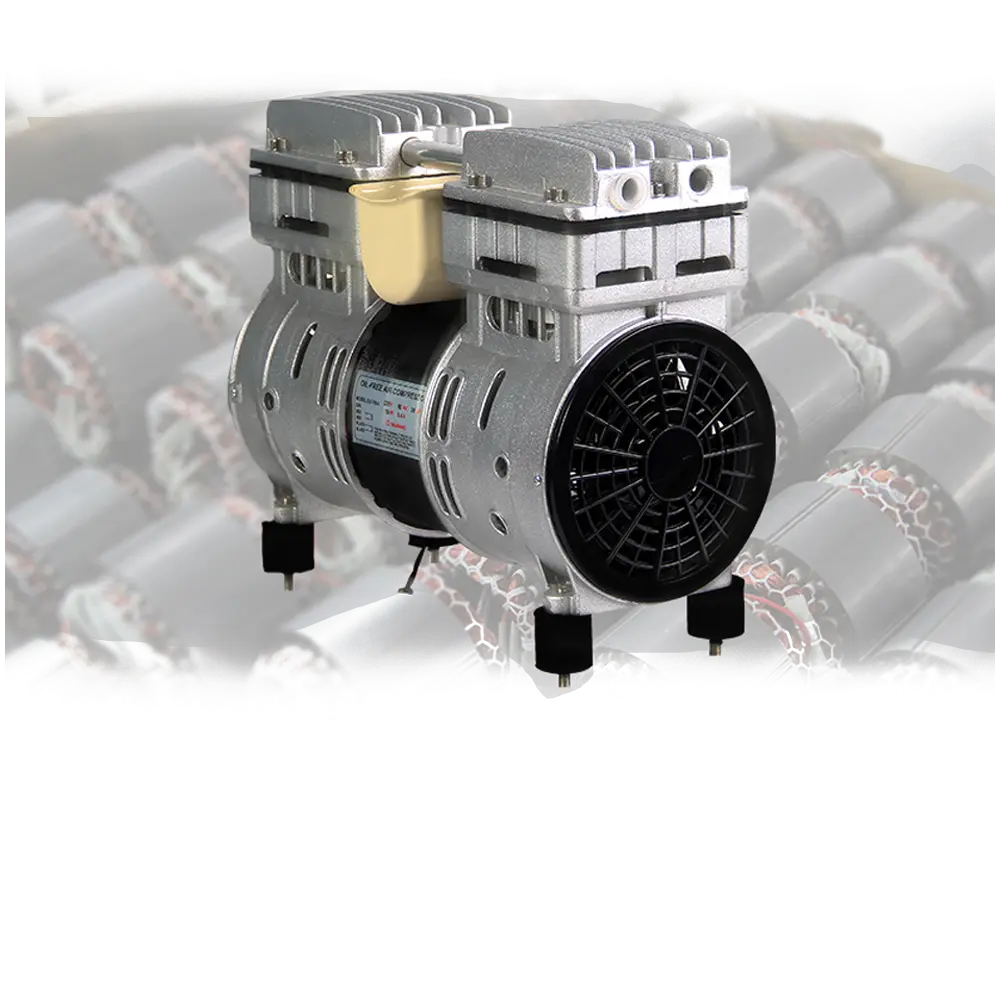
INCREASES SPEED AND REDUCES NOISE
Oil-injected air compressors require more power to heat up and start working because oil is viscous and difficult to get moving, especially in cold conditions. With an oil-free air compressor, that extra start-up time isn’t needed, so you can get production started without delay.
Another advantage of oil-free compressors is their ability to operate quietly. Some have sound levels as low as 48 dBA. Although sound isn’t the most important consideration for most facilities, it’s a bonus if your engineers and technicians are spending a lot of time near the machine throughout their workday.
Technical Specification
Model | Power KW | Cylinder MM | Working Pressure Mpa | Air Delivery m³/min | Measure L×W×H | Net Weight KG | ||
Lenth | Width | Height | ||||||
BNAP-OF550 | 0.55 | 2×63.7 | 0.8 | 0.06 | 290 | 130 | 190 | 10 |
BNAF-OF750 | 0.75 | 2×69.4 | 0.8 | 0.07 | 270 | 130 | 210 | 11 |
BNAF-OF1100 | 1.1 | 2×69.7 | 0.8 | 0.1 | 320 | 160 | 290 | 16 |
BNAF-OF1500 | 1.5 | 2×70 | 0.8 | 0.12 | 320 | 160 | 290 | 18 |